Mastering Quality Control in China: Strategies for Global Business Success
Navigate the complexities of ensuring product excellence with strategic quality control measures in China's dynamic manufacturing sector.
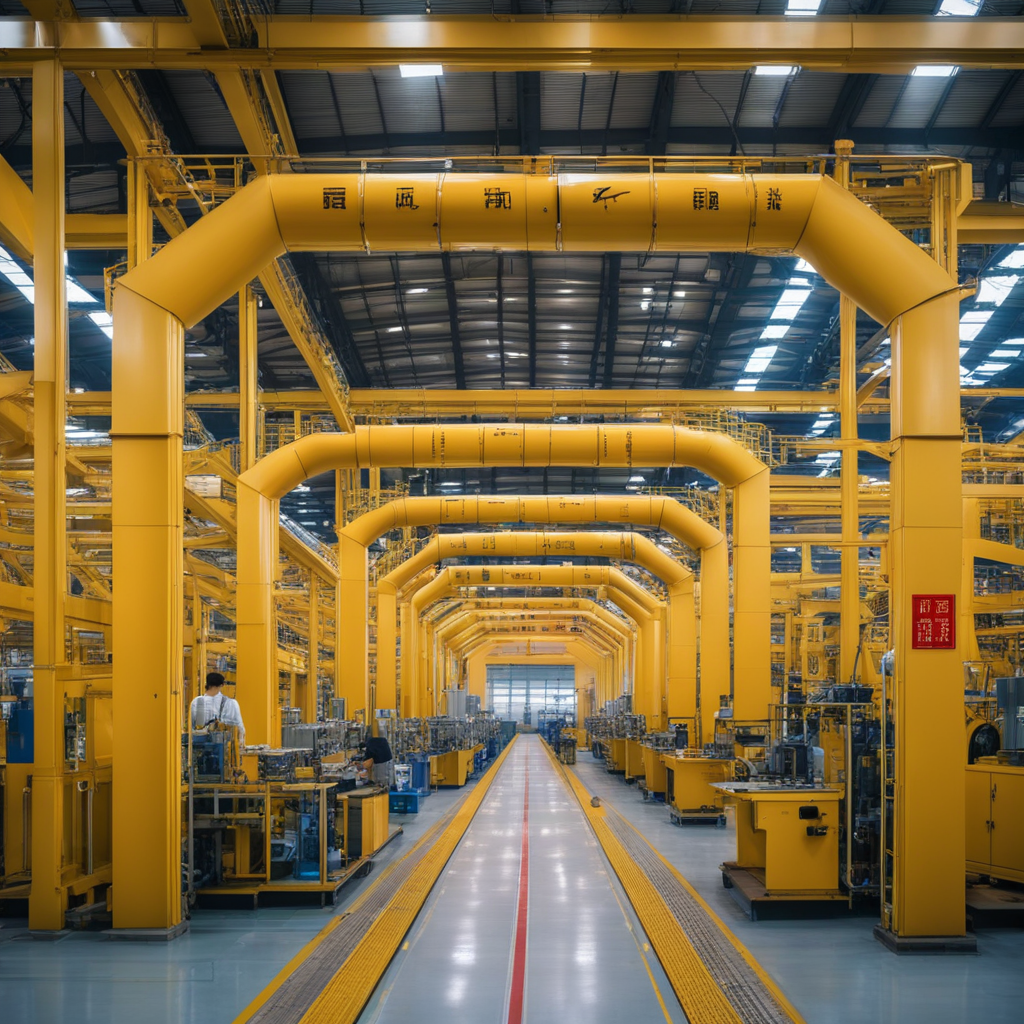
The Importance of Quality Control in China
China's significant role in global manufacturing is irrefutable, offering immense opportunities and inherent challenges in maintaining consistent product quality. Effective quality control in China transcends basic compliance, evolving into a strategic necessity that protects brand reputations, guarantees customer satisfaction, and ensures global market competitiveness. It's integral for businesses to view quality control not only as a regulatory requirement but as a cornerstone of operational excellence and innovation in a market known for its rapid pace and vast scale.
Understanding Quality Control Processes in China
Quality control in China entails rigorous activities aimed at detecting and addressing manufacturing defects, guaranteeing that products achieve stipulated quality and safety benchmarks. This comprehensive approach includes:
Overview of Standard Quality Control Procedures
At its core, quality control involves a series of steps including supplier evaluation, product inspections at various stages of production, and pre-shipment reviews. These procedures are aimed at preempting potential issues by embedding quality checkpoints throughout the production lifecycle. Utilizing an array of techniques, from random sampling to comprehensive product tests, these procedures form a meticulous framework designed to uphold product integrity from conception to delivery.
The Role of Third-Party Inspection Services
Third-party inspection services have emerged as indispensable allies for businesses seeking to fortify their quality control efforts in China. These independent agencies specialize in conducting unbiased inspections and audits, offering an external perspective on the adherence to quality standards and contractual obligations. Their expertise not only complements internal quality measures but also enhances transparency and trust between international buyers and Chinese manufacturers.
Compliance with International Quality Standards
The alignment with international quality standards, such as ISO 9001, is a testament to a manufacturer's commitment to quality excellence. These standards provide a universal benchmark that transcends geographical and cultural barriers, enabling businesses to navigate the complexities of global trade with confidence. Compliance with such standards is a proactive step towards integrating quality at the heart of production, fostering a culture of continuous improvement and aligning manufacturing outcomes with global expectations.
By demystifying the quality control processes prevalent in China, businesses can better prepare to engage effectively with suppliers and navigate the intricate landscape of Chinese manufacturing. The next sections will explore strategic implementations and solutions to common challenges, further empowering businesses to achieve quality excellence.
Effective Strategies for Implementing Quality Control
To optimize quality control in China’s manufacturing landscape, businesses must adopt a multi-faceted approach, emphasizing partnership with reputable suppliers, regular performance audits, and the integration of advanced technological solutions:
Partnering with Reliable Suppliers
The foundation of effective quality control lies in collaborating with suppliers that have a solid reputation for quality and reliability. Conducting thorough vetting, evaluating past performance, and visiting facilities in person are crucial steps in ensuring that a supplier’s values align with your quality expectations.
Conducting Regular Audits and Inspections
Implementing a regime of regular audits and inspections forms the cornerstone of proactive quality management. These assessments should not be viewed merely as obligations but as opportunities to identify areas for improvement, fostering a culture where quality is continuously enhanced.
Leveraging Technology for Quality Assurance
The advent of digital tools and platforms offers unprecedented opportunities for enhancing quality control measures. From real-time tracking systems to AI-driven quality inspection technologies, leveraging these innovations can significantly improve efficiency and accuracy in quality assurance processes.
Navigating Common Quality Control Challenges
Businesses often face obstacles such as cultural and language barriers, complex logistic networks, and stringent regulatory landscapes. Overcoming these challenges involves strategic communication improvements, advanced supply chain management, and compliance with local and international regulations, ensuring uninterrupted operations and quality assurance.
The Future of Quality Control in China
The evolution of quality control in China is marked by the integration of technological innovations and a growing focus on automated and digitalized manufacturing processes. These advancements promise to enhance quality control precision, offering solutions like IoT for real-time monitoring and blockchain for enhanced traceability. Preparing for this future requires businesses to invest in ongoing innovation, team development, and a commitment to elevating manufacturing standards.
Emerging technologies and a heightened emphasis on sustainability are reshaping quality control practices, aligning them more closely with global market demands and consumer expectations for ethical production. Embracing these trends positions businesses for success, ensuring they remain at the forefront of quality and compliance in the ever-evolving landscape of Chinese manufacturing.
By adopting a comprehensive and forward-thinking approach to quality control in China, businesses can not only safeguard their products' integrity but also reinforce their brand's reputation, unlock operational efficiencies, and secure a competitive edge in the global marketplace.