Deciphering the Expense: Understanding the Cost of Product Inspection for Electronics
Explore the costs and strategies behind electronics product inspection to ensure quality, reduce defects, and maintain competitive edge.
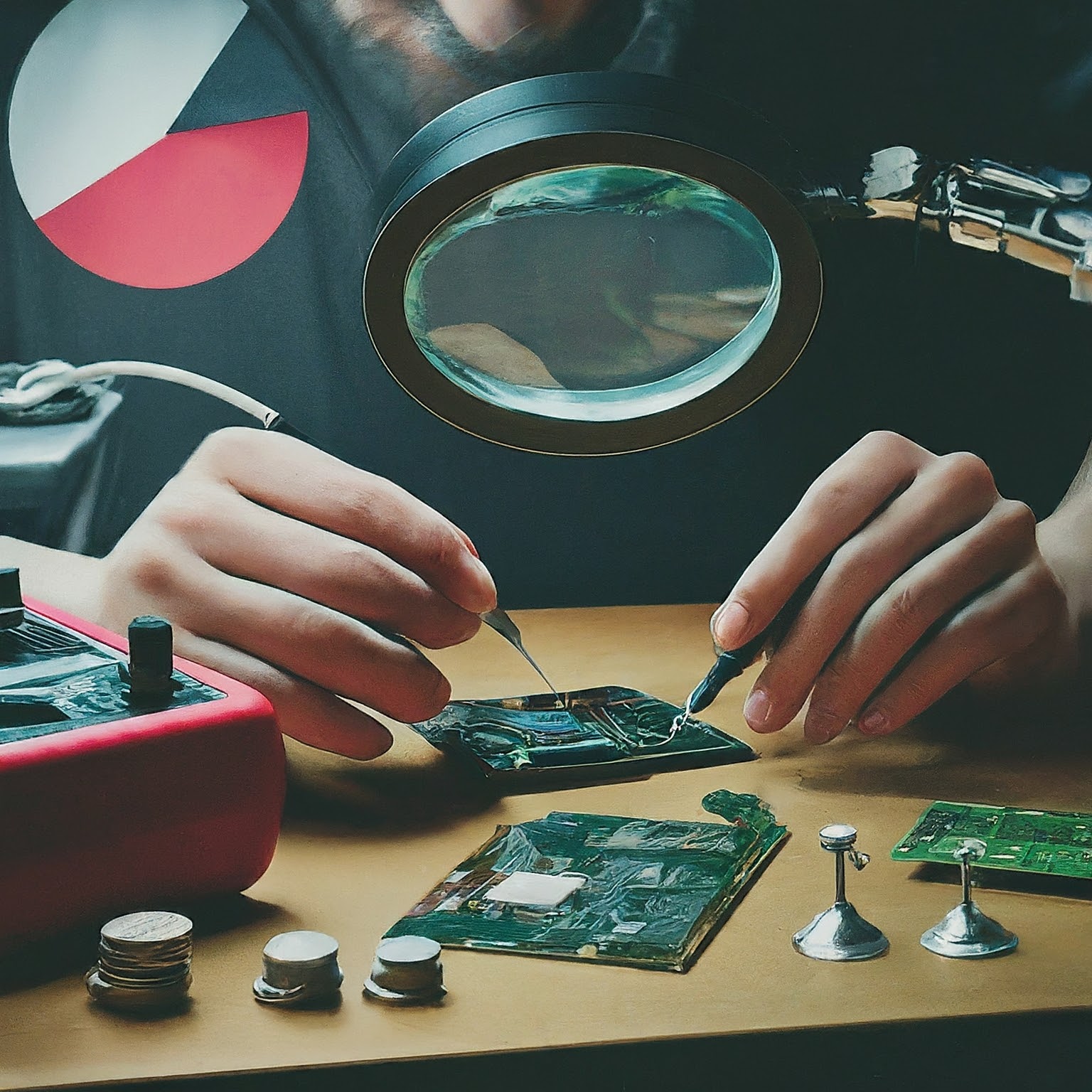
The Imperative of Product Inspection in the Electronics Industry
In the fast-paced realm of electronics manufacturing, product inspection stands as a critical safeguard, ensuring both consumer safety and product reliability. The intricate nature of electronic goods, coupled with their widespread usage in various critical applications, underscores the indisputable need for meticulous inspection processes. Unlike other industries, electronics bear the unique challenge of complying with a broad spectrum of regulatory standards, while also meeting the high expectations of a technologically savvy consumer base.
Electronics product inspection acts as a crucial checkpoint in the production lifecycle, identifying potential faults that could lead to product failure or, worse, end-user hazards. Given the complexity of electronic products, ranging from simple gadgets to sophisticated machinery, the inspection process becomes not just a matter of quality assurance but a comprehensive risk management practice. This pivotal process facilitates the detection of issues ranging from minor defects to critical malfunctions, ensuring that every product hitting the market is safe, functional, and up to the standards that both the industry and consumers demand.
Factors Influencing the Cost of Product Inspection
The cost associated with inspecting electronics is influenced by a myriad of factors, each contributing to the overall expense of the quality assurance process. Understanding these elements is paramount for manufacturers aiming to balance the scales of cost and quality optimization.
Complexity of the Electronics Being Inspected
The intricacy of the product under inspection plays a significant role in dictating the cost. Complex devices, endowed with advanced functionalities and components, demand more time, expertise, and sophisticated tools for a thorough inspection. These detailed evaluations necessitate highly specialized inspectors, further escalating the costs.
Scale of Production and Inspection Scope
The volume of production directly correlates with inspection costs. Large-scale manufacturing operations involve extensive quality checks, multiplying the overall expense. Additionally, the scope of the inspection—whether it encompasses a few critical components or a comprehensive review of the entire product—also influences costs.
Geographic Location of Manufacturing Facilities
The geographical setting of the manufacturing unit can significantly impact inspection costs due to variations in labor rates, operational expenses, and logistical aspects. Facilities located in regions with higher costs of living may incur greater expenses in conducting product inspections.
Required Certifications and Standards Compliance
Electronics often necessitate compliance with a host of international standards and certifications, which vary based on the product type and intended market. Achieving and maintaining these certifications involves rigorous inspection processes, including specialized tests that can add to the cost.
By dissecting the factors that influence the cost of electronics product inspection, manufacturers and stakeholders can better strategize on optimizing their quality assurance investments. Recognizing these cost drivers enables a more informed approach to planning and executing product inspections, ensuring that the end products not only meet the required standards but are also produced within a cost-effective framework.
Average Cost Ranges for Electronics Product Inspection
Determining the average cost of product inspection for electronics is not a one-size-fits-all scenario; it varies widely based on the factors previously outlined. However, manufacturers can anticipate certain cost ranges that help in budgeting and financial planning. For instance, basic visual inspections might range from a few dollars per unit for high-volume products to higher rates for low-volume, complex items requiring specialized scrutiny. In-depth inspections involving functional testing, certification compliance, and safety checks may see costs escalate, potentially reaching hundreds of dollars per unit for the most advanced electronic products.
It's crucial for businesses to consider these cost variations within the context of their production scale and the complexity of their products. High precision electronics destined for critical applications, such as medical devices or aerospace components, naturally entail higher inspection costs, justified by the need for uncompromised quality and reliability.
Balancing Cost with Quality: Maximizing Your Inspection Investment
For electronics manufacturers, the challenge isn't merely managing the cost of product inspections but ensuring that these costs translate into tangible quality improvements. Strategic investment in quality control can lead to reduced defects, fewer recalls, and enhanced brand reputation, justifying the initial expenditure. Partnering with reputable inspection services that can offer scalable solutions tailored to the product complexity and production volume can optimize the value derived from inspection costs.
Businesses can also maximize their inspection investment by focusing on critical control points in the manufacturing process that have the highest risk of quality issues. By prioritizing these areas, companies can deploy their resources more effectively, preventing potential defects before they occur. Adopting a continuous improvement mindset and utilizing inspection data to refine processes can further enhance product quality, reducing the long-term need for extensive inspections.
Future Trends: How Technological Advances May Influence Inspection Costs
The landscape of electronics product inspection is on the cusp of transformation, driven by advancements in technology. Automation, AI, and machine learning are set to revolutionize traditional inspection methodologies, potentially reducing the manpower and time required while increasing inspection accuracy and consistency. These technologies can identify patterns and predict potential failure points, facilitating preemptive quality control measures.
Moreover, innovations such as 3D scanning and augmented reality (AR) for remote inspections could drastically reduce logistical costs and enable more frequent quality checks without the need for physical presence. As these technologies become more prevalent and their costs decrease, electronics manufacturers will likely see a significant shift in the cost structure of product inspections, offering enhanced quality assurance at reduced costs.
Embracing these future trends and investing in technology-driven inspection processes will enable electronics manufacturers to maintain a competitive edge. By proactively adapting to these changes, businesses can ensure that their quality control mechanisms are not only cost-effective but also aligned with the increasing demands for exceptional product quality in the electronics industry.